Использование CAD-систем при разработке холодильных установок
Евгений ПРАСОВ, специалист по холодоснабжению
За последние 20 лет холодильная индустрия пережила множество изменений и нововведений, связанных с автоматизацией работы. Данные изменения не обошли стороной и людей, непосредственно связанных с разработкой холодильных комплектующих и элементов, в частности — проектировщиков и конструкторов.
Мне хотелось бы более подробно рассказать об использовании CAD-систем в проектировании и разработке холодильных машин. Итак, для начала стоит объяснить, что из себя представляет вышеуказанная система. CAD-система (Сomputer-Aided Design — компьютерная поддержка проектирования) — это система автоматизированного проектирования, предназначенная для выполнения проектных работ с применением компьютерной техники, а также позволяющая создавать конструкторскую и технологическую документацию на отдельные изделия, здания и сооружения. Также для обозначения подобных систем широко используется аббревиатура САПР (система автоматизации проектных работ). Основная цель CAD-системы — повышение эффективности труда инженеров за счет автоматизации работ на стадиях проектирования и подготовки производства. В качестве входной информации CAD использует технические знания специалистов, которые вводят проектные требования, уточняют результаты, проверяют полученную информацию опытным путем.
Система автоматизированного проектирования реализуется в виде комплекса прикладных программ, обеспечивающих проектирование, черчение, трехмерное моделирование конструкций плоских либо объемных деталей. Как правило, в современные CAD-системы входят модули моделирования трехмерной объемной конструкции (детали) и оформления чертежей и текстовой конструкторской документации (спецификаций, ведомостей и т. д.).
В холодильной технике данные программы себя очень хорошо зарекомендовали за счет того, что практически все производители холодильного оборудования и комплектующих в своих конструкторских подразделениях работают в данной системе и всегда готовы предоставить инжиниринговым компаниям 3D-модели своей продукции, что упрощает создание базы используемых элементов и кардинально экономит время на разработку, поскольку завод-изготовитель предоставляет исходный файл с габаритами, полностью соответствующими готовому изделию.
Рис.Эскиз трубопровода
Рис. Автоустановка отводов
Конструктору остается только создать базу трубопроводов и сварных конструкций. Рассмотрим принцип работы более детально. Имея все необходимые 3D-модели используемого оборудования, в первую очередь начинается разработка гидравлической части холодильной машины, то есть схематическая установка компрессора, различных клапанов и всех сопутствующих элементов. После необходимой расстановки мы можем приступать к прокладыванию трубопровода. Заранее создав базу всех диаметров труб, отводов, тройников, муфт и т. д., программа автоматически будет сама определять установку необходимого элемента. Наша задача заключается только в том, что мы должны линиями показать направления труб и в зависимости от диаметра выбрать использование отводов или гибку трубы. Кроме того, имеется функция автомаршрут, когда программа сама прокладывает трубопровод по кратчайшему пути, что также экономит время при проектировании.
Единственное, что конструктор должен выполнять вручную — это установку переходов (редукторов), изменяющих диаметры трубопровода в нужных для этого местах (после установки программа автоматически меняет значения трубопровода «по умолчанию» и в последующих действиях стандартным трубопроводом будет использоваться измененный диаметр, прописанный в настройках перехода). Также существует дополнительная функция для трубопровода — наличие изоляции (теплоизоляции), то есть в момент создания трубопроводов конструктор может задать необходимую толщину теплоизоляции (для трубопроводов низкого давления, которые подвержены обмерзанию во время работы холодильной установки), и в итоговой спецификации данные элементы будут разделены между собой (труба и изоляция заданной толщины).
Рис. Агрегат в сборе
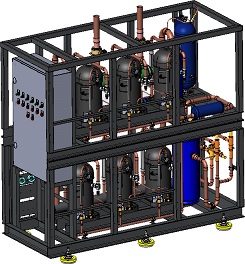
Рис. Сварная конструкция
После того как создана вся гидравлическая часть, конструктор преступает к разработке несущей станины (рама или корпус). Принцип построения схож с трубопроводом, только уже вместо диаметров труб используются эскизы сварных элементов (швеллер, труба, уголки, двутавры и т. д.). Принимая модель гидравлической части как базовый элемент, выполняется эскизный «скелет», то есть построение огромного количество линий под местами необходимой фиксации, которые в последствии будут преобразованы в профили. Также к данному разделу хотелось отнести и работу с листовым металлом.
Листовой металл в основном используется при создании корпусных изделий и различного типа стоек. Для оптимальной и точной работы с данным разделом необходимо знать таблицы гибов и коэффициент Пуассона гибочной машины (эти данные всегда идут в техническом паспорте установки).
Рис. Развертка
Внеся эти данные в программу, мы задаем строгие параметры операций при создании детали, которые будут заблокированы для последующего редактирования, то есть программа автоматически имитирует процесс гибки на гибочном станке. Также перед гибкой необходим исходный файл развернутой на плоскости поверхности геометрического тела для выреза его из листового металла. В функции программы входит данная операция. После окончания создания изделия в 3D необходимо только выбрать операцию «развертка», по окончании которой мы получаем форму листа, который нам необходим для гибки с учетом всех радиусов гибки.
После окончания разработки 3D-модели холодильной машины необходимо составить спецификацию всех использованных в ней элементов. Данная операция выполняется автоматически, программа также сразу указывает позиции, обозначающие месторасположение конкретного элемента с его наименованием и необходимыми данными, как приведено ниже на рисунке (на примере нижнего яруса рамы).
Рис. Проверка потока жидкости
Какие данные должны быть отображены в спецификации, — выбирает сам конструктор. Если внести в свойства каждого элемента его стоимость, то в итоге на конечной спецификации будет указана и общая себестоимость разработки, определенная по сумме всех комплектующих. Тем самым конструктор может частично выполнять функцию экономического сектора. Данная система предназначена также для сокращения затрат на натурное моделирование и испытания за счет использования модулей, имитирующих различного типа нагрузки. К примерам можно отнести:
• проверку несущей станины на деформацию за счет установленных на ней элементов, то есть выдержит ли заложенный металл всю массовую нагрузку, с получением отчета и цветовой схемой.
• проверку состояния потока жидкости/газа в трубе на потери/избыток давления или температуры и проч.
Подведя итоги, хотелось бы перечислить все плюсы использования данной системы при разработках холодильного оборудования:
• сокращение трудоемкости проектирования и планирования;
• сокращение сроков проектирования;
• сокращение себестоимости проектирования и изготовления, уменьшение затрат на эксплуатацию;
• повышение качества и технико-экономического уровня результатов проектирования;
• сокращение затрат на натурное моделирование и испытания.
Достижение этих целей обеспечивается путем:
• автоматизации оформления документации;
• информационной поддержки и автоматизации процесса принятия решений;
• использования технологий параллельного проектирования;
• унификации проектных решений и процессов проектирования;
• повторного использования проектных решений, данных и наработок;
• стратегического проектирования;
• замены натурных испытаний и макетирования математическим моделированием;
• повышения качества управления проектированием;
• применения методов вариантного проектирования и оптимизации.