Проблемы при эксплуатации холодильного оборудования и их решения
Николай ЖУК, эксперт АПИМХ, советник МАХ
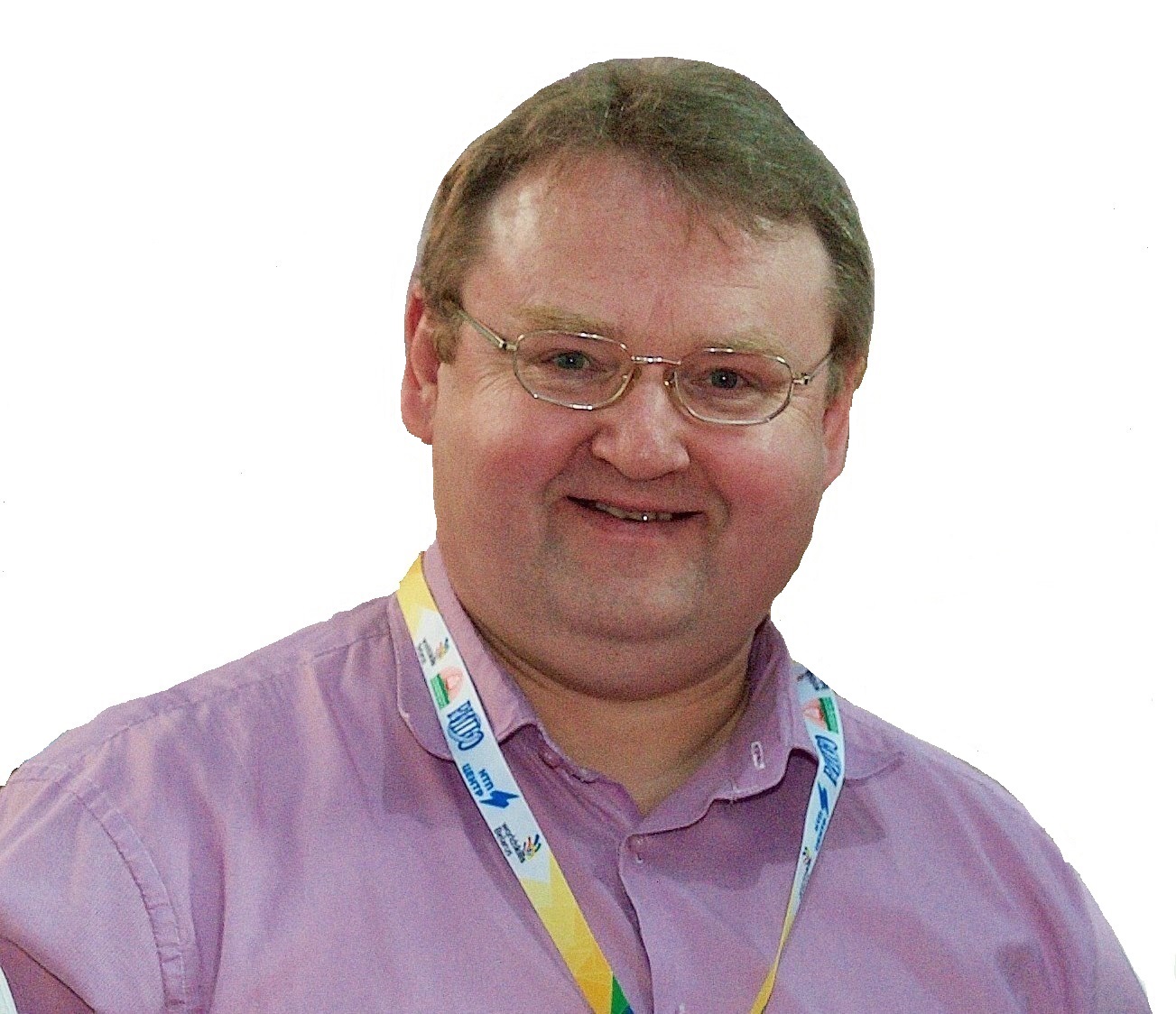
Мы продолжаем ранее начатую рубрику, где эксперты АПИМХ делятся опытом проведения экспертиз на реальных объектах и конкретных фактах выхода из строя холодильного оборудования. Проблема достаточно широка, чтобы ее можно было осветить в одной публикации, поэтому этой тематике отводится цикл статей. Напомним, что в предыдущем номере журнала более детально рассматривались вопросы, связанные с ошибками при выборе и комплектовании холодильных систем.
Ошибки при монтаже и наладке оборудования
Как правило, к качеству монтажа основного агрегатированного оборудования меньше претензий, хотя и здесь ошибок хватает. Задача инженерной службы — выявить такие ошибки до проведения монтажных работ. Но это тема отдельного разговора. Хотелось бы в рамках данной статьи уделить внимание несколько другому, а именно — типичным нарушениям при проведении пусконаладочных операций.
Испытание на прочность и герметичность
Главным и первоочередным в ряду операций на завершающем этапе монтажа является испытание смонтированных трубопроводов холодильной установки на прочность и герметичность. Основная цель этих операции — как раз выявление мест утечки. Неправильное проведение данных процедур, а зачастую и их полное отсутствие, приводят к необоснованным потерям холодильного агента через вовремя необнаруженные места негерметичности, часто вплоть до того момента, пока не выйдет из строя компрессор.
Сама процедура испытаний на прочность и герметичность вполне подробно и корректно описана в учебной литературе и в нормативных документах. Так, в ГОСТ EN 378–2014 указан порядок проведения испытаний холодильного оборудования и комплектующих.
Проведение испытаний должно в обязательном порядке подтверждаться документально с указанием времени его начала и окончания, вещества, используемого для испытаний, давления и температуры в начале и конце испытания. В качестве основы можно принять требования, указанные в ТКП 45-3.05-167–2009, где описаны процедуры проведения испытаний. Кстати, здесь же указаны требования к монтажу трубопроводов холодильных установок, а в приложениях имеются типовые акты испытаний технологических трубопроводов, в частности, дополнительного испытания на герметичность. В эту форму акта можно внести строку для указания температуры окружающей среды в процессе проведения испытания, а оно должно длиться не менее 24 ч.
При проведении испытаний потребуется убедиться, что падение испытательного давления связано только со снижением температуры окружающей среды, а не с утечкой. Для этого выполняется перерасчет давления по известной формуле Шарля: Р1/Т1 = Р2/Т2 (где давления Р и температуры Т соответственно в начале и конце испытания подставляются в абсолютных значениях). Для точного контроля давления не стоит пользоваться манометрами с широким диапазоном шкалы (более 20 бар), так как уловить изменения давления в десятые доли барии будет проблематично. Для этой цели идеально подойдут цифровые манометры и термометры.
Правильное проведение испытаний и своевременное оформление соответствующей документации гарантируют в первую очередь герметичность системы. Это также снизит риск возникновения проблем и непониманий в дальнейшем при работающем оборудовании, поскольку возникшие утечки, скорее всего, будут рассматриваться, как последствия некачественной эксплуатации, а не появившиеся по вине монтажников.
Вакуумирование
Второй процедурой, от качественного проведения которой зависит дальнейшая корректная работа холодильной установки, является вакуумирование всей системы трубопроводов. Необходимо четко понимать, что цель вакуумирования — удаление из системы газов и влаги. Вакуумирование ни в коем случае не является испытанием на герметичность, испытательные процедуры которого описаны ранее. На этот счет много сказано во всех возможных источниках информации. Хотелось бы заострить вопрос на некоторых нюансах, при незнании и непонимании важности которых качественное вакуумирование, особенно удаление влаги, не произойдет.
Первое: при вакуумировании необходимо открыть все ручные и электронные запорные и регулирующие устройства для удаления газов из всех участков трубопроводов. Следует очень внимательно изучить схему трубопроводов и наличие всех возможных устройств, которые могут быть перекрыты при давлении в системе, ниже рабочего, в том числе и при вакуумировании. Почти никогда не забывают открыть ручные запорные вентили (шаровые или другого типа), проконтролировать это не представляет труда. Особое внимание нужно уделить соленоидным вентилям, которые можно открыть либо при их включении (что не всегда возможно из-за сложной схемы электрических соединений), либо с использованием специального кольцевого магнита (но он есть не у каждого наладчика). Надеяться на то, что за счет перепада давления произойдет открытие вентилей, и все участки трубопровода будут отвакуумированы, не приходится. При наличии в системе пружинных регуляторов давления (например, регуляторы давления кипения, конденсации, в картере, в ресивере) бывает сложно определить, в каком положении они находятся и как поведут себя при создании вакуума с какой-либо стороны. Поэтому при вакуумировании необходимо обеспечить их полное открытие и уже при работающей установке по-новому перенастроить. Такую же злую шутку могут сыграть и обратные клапаны на трубопроводах, а также клапаны компрессора, которые могут закрыться при создании вакуума не с той стороны. Не зря рекомендовано при вакуумировании подключаться к обеим сторонам трубопроводной системы, а лучше — в нескольких точках. Или, если это невозможно, то, продвигаясь по трубопроводам, последовательно открывать запорные устройства, четко понимая, в каком положении они находятся при создании вакуума с конкретной стороны. При соблюдении этих несложных рекомендаций обеспечится тщательное удаление газов и влаги из всей системы, а это — гарант продолжительной работы холодильной установки в дальнейшем.
Второе: обязательное проведение процедуры срыва вакуума при первоначальном вакуумировании новой установки, иногда эту процедуру называют осушкой системы или промывкой, что технически более правильно. Она заключается в неоднократном (два – три раза) чередовании вакуумирования и частичного заполнения системы азотом (или хладагентом) с последующим окончательным вакуумированием. Для чего это делается? Общеизвестно, что при создании соответствующего вакуума вода превращается в пар, который должен быть удален из системы вакуумным насосом, — это главная цель вакуумирования. Однако при уже созданном вакууме не все пары и газы смогут перемещаться по трубопроводам в сторону насоса, так как уже нет перепада давления, и движение в трубопроводах отсутствует. Поэтому газы могут остаться и не удалиться вакуумным насосом. При заполнении системы азотом происходит перемешивание оставшихся газов с ним, которые вместе стравливаются в атмосферу, а далее система опять вакуумируется насосом. Если провести такую процедуру два раза, а лучше — троекратно, можно с уверенностью гарантировать чистоту (или осушку) системы.
Третье: соблюдать достаточную продолжительность вакуумирования. Четкого времени вакуумирования в документации не указано. Каждый монтажник обычно это время устанавливает исходя из собственного опыта. Наиболее точно время вакуумирования можно определить электронным вакуумметром, который указывает температуру испарения воды при конкретном вакууме и обеспечивает достижение цели вакуумирования — полное удаление из системы паров воды. В любом случае можно с уверенностью сказать: чем дольше проводится вакуумирование, тем лучше.
Соблюдение вышеперечисленных рекомендаций гарантирует проведение качественного вакуумирования в достаточно короткие сроки. Если систему оставить под вакуумом на сутки с контролем вакуума, то можно проследить процесс доиспарения воды и убедиться, что вакуумирование проведено качественно. Оформить документально процедуру вакуумирования и контроля под вакуумом можно точно так же, как и проведение испытаний давлением.
Заправка установки хладагентом
Выполнение вышеперечисленных процедур позволяет перейти к следующим этапу — заправке системы хладагентом. На этой стадии также возможны ошибки. Наиболее просто осуществляется заправка заводских систем с точным указанием требуемой массы заправки, как правило, с капиллярной трубкой в качестве дросселирующего устройства.
Если монтаж трубопроводов к испарительным системам, оборудованным терморегулирующими вентилями, проводится по месту, появляется необходимость контроля массы заправки хладагента в процессе пусконаладки. Конечно, норму заправки можно просчитать, но в любом случае потребуется ее уточнение. Наиболее точным способом определения нормы заправки является контроль переохлаждения на конденсаторе и перегрева на испарителе холодильной установки. Для этого необходимы достаточная квалификация монтажника и наличие соответствующих измерительных инструментов. К данному интересному этапу мы обратимся в последующих публикациях.
Здесь хотелось бы отметить, что зачастую количество заправленного холодильного агента остается на совести монтажников, которые в нарушение требований EN 378–2014 никакой документации не ведут, журнал учета технического состояния системы вместе с Актом ввода в эксплуатацию оборудования не оформляют и заказчику не передают. Это пугающая тенденция, которую необходимо всячески искоренять. В дальнейших статьях мы будем поднимать вопросы ведения документации.
Итак, понятно, что четкое соблюдение всех перечисленных операций обеспечит качественную эффективную работу холодильной установки, предотвратит потери дорогостоящего хладагента. Для этого потребуется много времени и усилий — в первую очередь от будущих владельцев оборудования, которые зачастую второпях поощряют горе-мастеров, работающих по принципу: зачем проводить опрессовку, я в своей работе уверен, быстренько отвакуумировал (минут эдак 5–7!), заправил по минимуму (сэкономил) и все — пользуйся владелец. Воздух и вода остались внутри, окислилось масло, пошла коррозия, вышли из строя теплообменные аппараты, сгорели обмотки электродвигателя, а все равно крайним будет, как ни странно, владелец, которому откажут в гарантийной замене оборудования.
Надеемся, что предоставленная информация послужит определенным стимулом к наведению порядка в холодильной отрасли, для повышения ответственности специалистов к своим обязанностям и выполненной работе. Также думаем, что и владельцы оборудования с большей скрупулезностью будут выбирать подрядчиков для выполнения работ, более строго контролировать ведение соответствующей документации, понимая поднятые в статье проблемы.
Копирование и переработка любых материалов этого сайта для публичного использования их (размещение на других сайтах, публикации в печатных изданиях, размещение в электронных СМИ и проч.) разрешается исключительно при получении письменного согласия Дирекции АПИМХ (017) 357 43 32, e-mail: apimh@tut.by